Construction industry challenges and solutions
The construction industry presents owners, managers, workers, contractors, and more with an
extensive list of potential problems. While it’s one of the most lucrative sectors in the entire
economy, still booming into 2024, traditional construction also creates razor-thin margins. Profits can be high, but the smallest issue can derail your project and payments.
Here are the top challenges and how they may impact your business, your workforce, and your profits.
Delays
The word “delay” is a dirty word on a construction site. Delays are perhaps the most common
issue, and they impact everyone on the job. Of course, delays can be caused by numerous
issues, including poor project management, unexpected labor problems, issues with the supply chain, accidents, and weather. From start to finish, delays can be caused by numerous factors. They can begin in the home office or they can be created at the job site.
Sometimes delays cause additional issues, such as fines, new supply chain issues, additional labor problems, etc. Of course, it can also cost additional expenses (such as additional labor and rental equipment) and erode profits.
That’s why project management is so important in the construction industry. (Hail great project managers!) Great construction project managers don’t just have a plan A, they have a plan B – Z, knowing how to mitigate issues and resolve challenges that may arise.
It’s also why modular construction (also known as offsite construction) is becoming so popular. Many components are built in a warehouse or facility that’s covered, and unaffected by inclement weather.
Errors in documentation
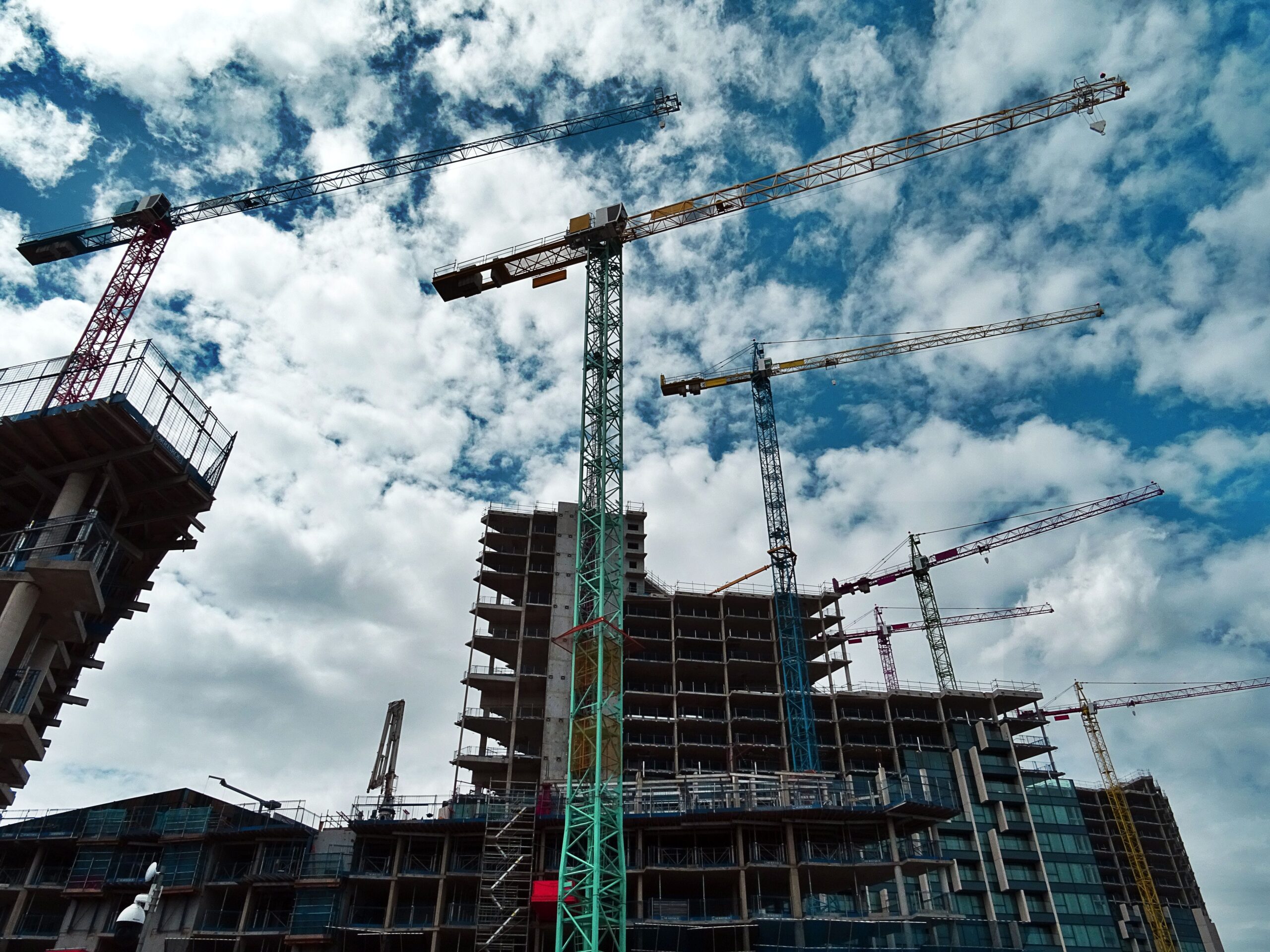
The size, scope, and complexity of construction projects are changing. Both commercial and
residential construction projects are seeing increases in efforts to speed up the process; ironically those changes are causing costly errors. Errors and omissions in overall documentation, especially during the preconstruction process, can mean increased costs and schedule delays.
Documentation errors can occur at numerous levels. Contract documents, drawings, pay applications, change orders, and submittals can all hold errors. When errors are found, it means rechecking details, refining contracts, communicating adjustments to personnel, and, on occasion, refining construction plans.
Our advice? Read, re-read, and re-read again your documentation. Have more than one person sign off, too … even for smaller projects.
Contract changes (yup, change orders)
Changes affect the time, scope, resources, materials, and cost of a project.
You know even the most simple change order may trigger a chain reaction of events, impacting numerous contractors and their teams. Occasionally, subcontractors make changes to the contract and begin working on the modification before they have approval to do so. This situation, which is all too common, can create payment disputes between the contractor and the owner or manager.
Planning and communication can help solve this issue, including determining who has authorization for a change. When more effort is spent reviewing site conditions and drawings, and there is a clear, mandatory process for making changes, the chance of this issue is significantly reduced.
Subcontractor closes their business
Subcontractors are running a business, too. And as we all know, they can face issues and have to close business. If a subcontractor fails in the middle of a project, construction owners and managers are left scrambling to fill the gap. As construction projects become more complex, there is an increase in the number of contractors, which increases the chances of a subcontractor default. The entire project can come to a halt until subcontractor issues are addressed and a new sub is found to fill the void.
Labor shortages and unions
Finding reliable, qualified labor is a challenge for every industry. For the construction field, it’s
one of the most frustrating and continuous challenges in the sector. Sadly, it’s not just your staff that you need to worry about. Will subcontractors have enough manpower to get the work they promised done? If not, your project could be in jeopardy.
If you have a union-based project, you have the potential for strikes that could slam the brakes on a project.
Improper forecasting
The construction industry may rely on planning, forecasting, and proper budgeting more than
any other sector. But it’s not easy and it’s rarely 100% accurate. Improper forecasting can create
unattainable goals and expectations, while improper budgets can significantly harm long-term
profits.
Although there isn’t a perfect solution to forecasting issues, it helps to break down the planning
into small segments (as small as reasonable) and focus meticulously on each task. This will provide better detail and clarification throughout construction.
Health and safety issues
It will come as no surprise that the construction industry is one of the most dangerous professions in the world. Falls, equipment misuse, vehicle accidents, and electrocution are just a few of the risks in this high-paced, high-pressure industry. But it’s not just accidents that cause immediate injury. Dust inhalation, loud noises, high/low temperatures, and more can create serious issues for a construction team.
Of course, following OSHA guidelines is a must. Also, listening to your employees on safety matters can make a huge difference. Your workers will know some of the risks maybe even before your quality or risk manager does.
Construction solutions
At Elevated, we wish we could promise a seamless construction process for every project. Although we can’t, we can help with material supply chain issues and help you stay on top of needed supplies. For example, we have safety gear to protect your workforce — we provide high-visibility apparel, hard hats, glasses, ear protection, gloves, and more. Elevated even has stocking agreements to ensure you never run out of a necessary supply. We also work with suppliers, such as OSI, who train your workforce and subcontractors on the best ways to use products. And we have ideas to streamline your processes to hit your deadlines and budget.