Modular construction expanding into major cities
If anything could revolutionize building practices, reduce the housing crisis, make new homes more affordable, and alleviate the construction labor shortage, modular construction might be the solution.
Also known as offsite construction, it’s the building and manufacturing parts of a home or facility in a controlled factory setting. This process enhances overall efficiencies by using the same materials and designs to create multiple versions of the same building section. Essentially, it streamlines the building process by manufacturing “modules,” which are then shipped to and assembled at the job site.
This type of construction is gaining traction all across the country, but it’s becoming a standard practice in certain cities and regions. Here are the top cities leading the way in modular construction….
New York City
As our nation’s largest and most densely packed metro area, New York City and the surrounding area have numerous housing challenges. City leaders have created a comprehensive plan to address these challenges and create more housing. One strategy they want to implement is modular housing.
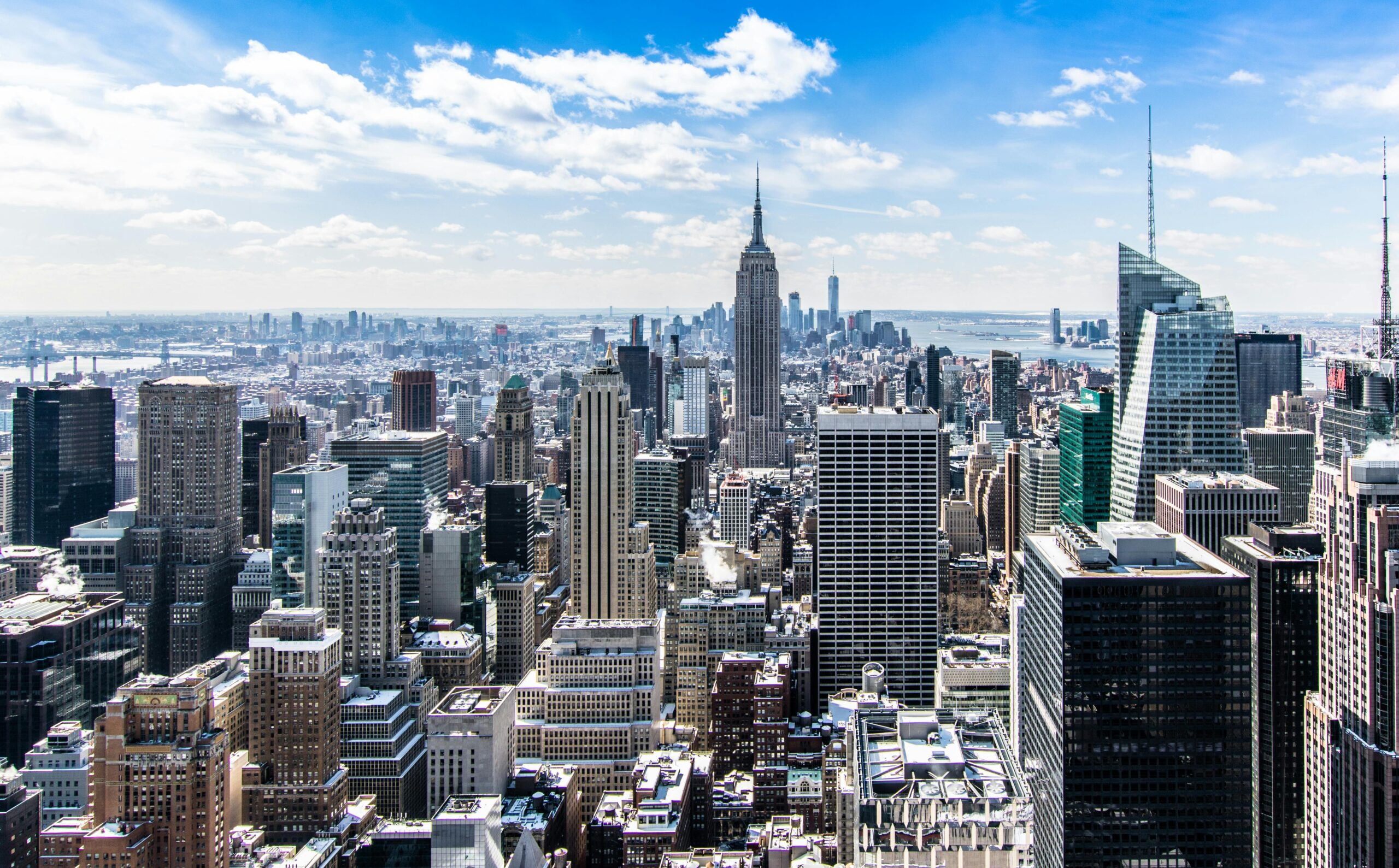
New York City has launched a modular construction initiative in the “Build It Back” program. The goal is to construct nearly 100 single-family modular homes, which, they believe, will bring a per-home cost savings of roughly 25%. Carmel Place, New York’s first micro-unit apartment building, opened in 2016 and includes 55 micro units.
Los Angeles
On the other side of the country, the City of Angels has its housing issues. Los Angeles has dealt with skyrocketing homelessness; estimates are reaching over 66,000 homeless individuals in the area.
L.A. recently completed the Hilda L. Solis Care First Village, a container-based supportive housing development with 232 beds. This modular-based facility should help alleviate homelessness throughout the area while allowing people to stay in safe, comfortable shelters.
Chicago
The Windy City provides an example of how regulations and building standards while serving an important purpose, can hamper modular construction and narrow its benefits. It also shows how removing outdated barriers to modular construction creates a path to faster, more affordable housing in a housing-tight market.
Chicago has attempted to increase modular homes by removing legal and regulatory barriers. However, state laws are still in effect. The Modular Building Institute cites a recent project involving three-unit apartment buildings. These buildings met the city standards, but when Illinois standards were applied, the per-unit cost rose by as much as $10,000. There is now an effort to remove these state barriers, which will help Chicago, the nation’s third-largest city, become a leader in modular construction.
Salt Lake City
The capital of Utah has become one of the fastest-growing cities in America. This growth brings certain challenges, including housing availability and affordability. According to Redfin, a major real estate listing and information website, the median sale price for a Salt Lake City home in 2020 was below $400,000. The price has gone through ups and downs, but the latest data has the median sale price at nearly $600,000. 42.9% of all homes are sold above the list price.
This pricing escalation has squeezed the average buyer, but modular homes could provide a solution. However, like most cities, there are regulatory restrictions. Essentially, all new construction must be inspected in Salt Lake City, but modular buildings are built, in large part, at out-of-state facilities. The city has now created a modular program that allows third-party agencies to conduct inspections on the city’s behalf. This will remove a significant barrier and, hopefully, result in more modular buildings throughout the city.
Seattle
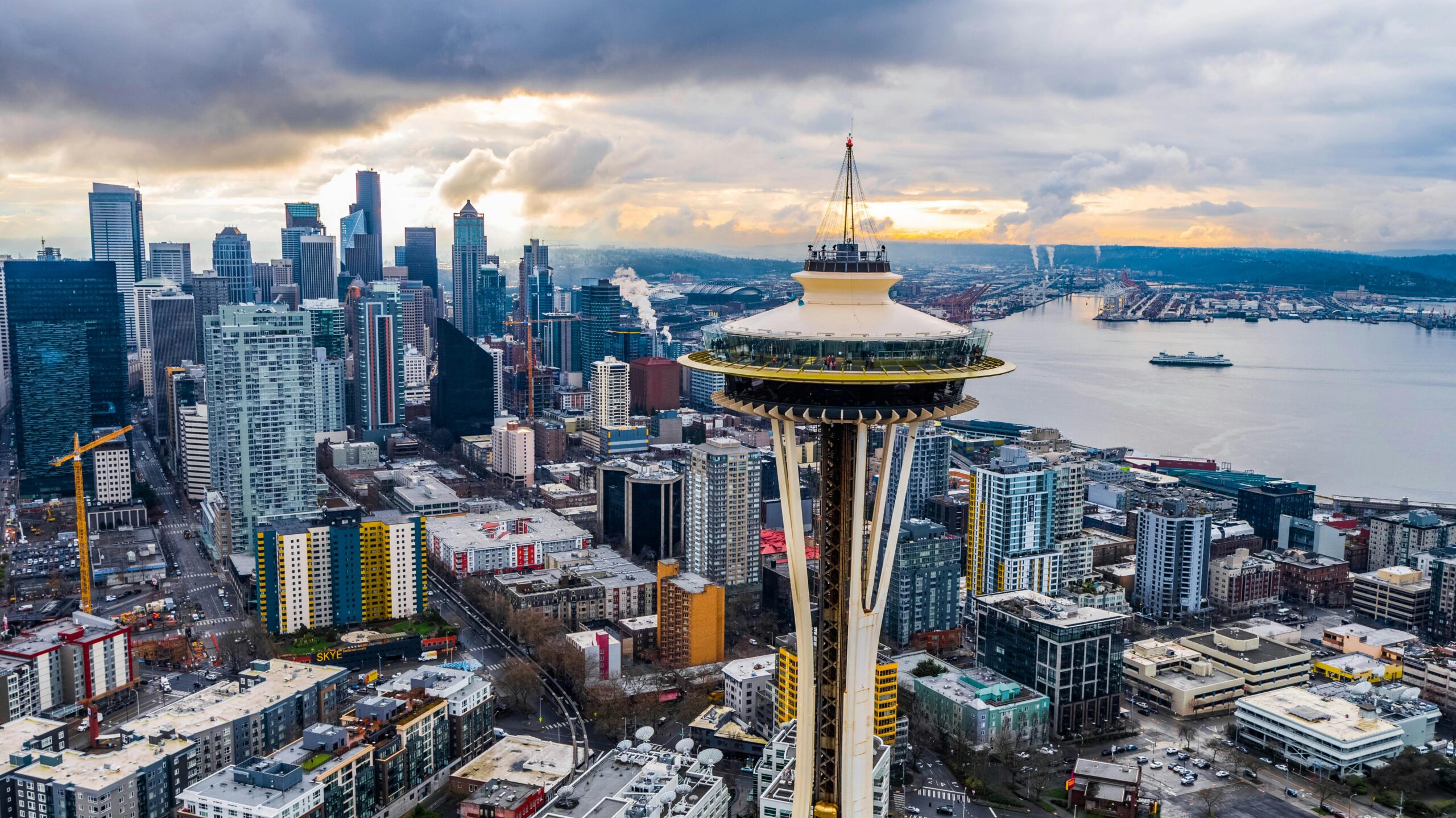
Not all modular construction includes homes and apartments. Some of the buildings are office or commercial spaces; the hospitality industry has benefited from modular. The Seattle South Lake Union Hotel is a fine example. This unique hotel, which won an award for Modular Building Design from the Modular Building Institute, comprises two traditional (on-site) stories and six levels of guest rooms made from modules. It is a cost-effective building, praised for architectural beauty, innovation, and sustainability.
Seattle has also seen the addition of a 112-unit apartment facility made from panels with pre-installed heating, electrical, and plumbing equipment. All of these panels were built at an in-state facility.
Twin Cities, Minnesota
Minneapolis, St. Paul, and the surrounding suburbs are also highlighted by rising housing costs and reduced real estate inventory. Like many other areas, they are also dealing with homelessness, which is impacted by the real estate market. Modular construction has been adopted in some areas to address these concerns.
NBA player and North Minneapolis native Devean George has helped remake one corner of the Twin Cities metro area by supporting modular construction, which he believes will ease the housing crisis. Modular construction is especially useful in Minnesota, where long winters limit the building season. Offsite construction also brings predictability, speed, and year-round fabrication, which are crucial in Minnesota and the upper Midwest.
Toronto
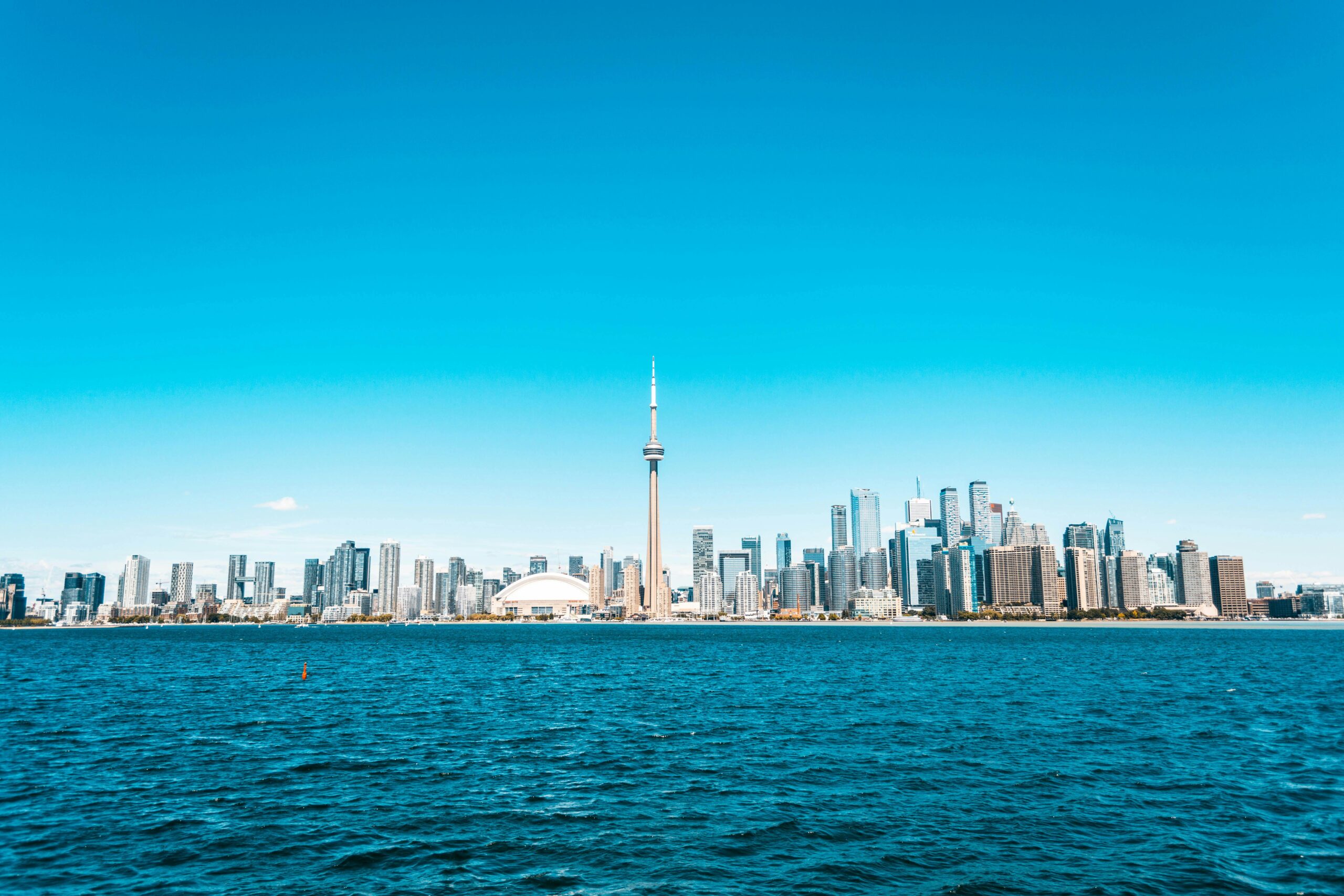
Modular construction is not just a trend in the U.S. Across the Canadian border, cities like Toronto are adopting these techniques to increase housing costs and reduce homelessness. Toronto is awarding multiple contracts to build modular facilities, giving builders access to standardized products that are easier for governments to plan long-term.
To increase speed, the city’s first modular project was based on a previous design, which streamlined cost and made construction more affordable.
Making your modular construction more efficient and profitable
At Elevated, we’ve been helping modular construction companies for more than ten years get the right tools, industrial supplies, appliances, PTACs and HVACs, and more. We’ll have ideas for your company on how to speed up the process, save money, and meet tight deadlines.