Interest rates forecast + construction and manufacturing
Interest rates vary by industry, lender, borrower, loan type, etc. However, almost all interest rates are affected by the Federal Reserve, which sets the rate that banks use to lend money to each other. This rate is known as the “fed fund rate,” and it influences all other loans.
So while the Federal Reserve doesn’t have direct control over, say, mortgage or auto-loan interest rates, their decisions wield a strong influence.
The Federal Reserve has two specific goals: increasing employment and creating stable, affordable prices. They attempt these objectives by changing rates to fit specific situations. When the market is seeing rapid inflation, it’s often because overall demand for products and services is too high. To ease this demand, they may increase rates and try to cool the market. However, if the market is stagnant, they may lower rates, which would (in theory) stimulate economic activity and overall demand.
(This, we admit, is a far-too-simple explanation of the Federal Reserve and interest rates.)
Decisions made by the Federal Reserve have a massive impact on many industries, including manufacturing and construction. If you work in these industries, it helps to understand what the Federal Reserve will do, why it will do it, and what impact it will have on your business.
Interest rates forecast
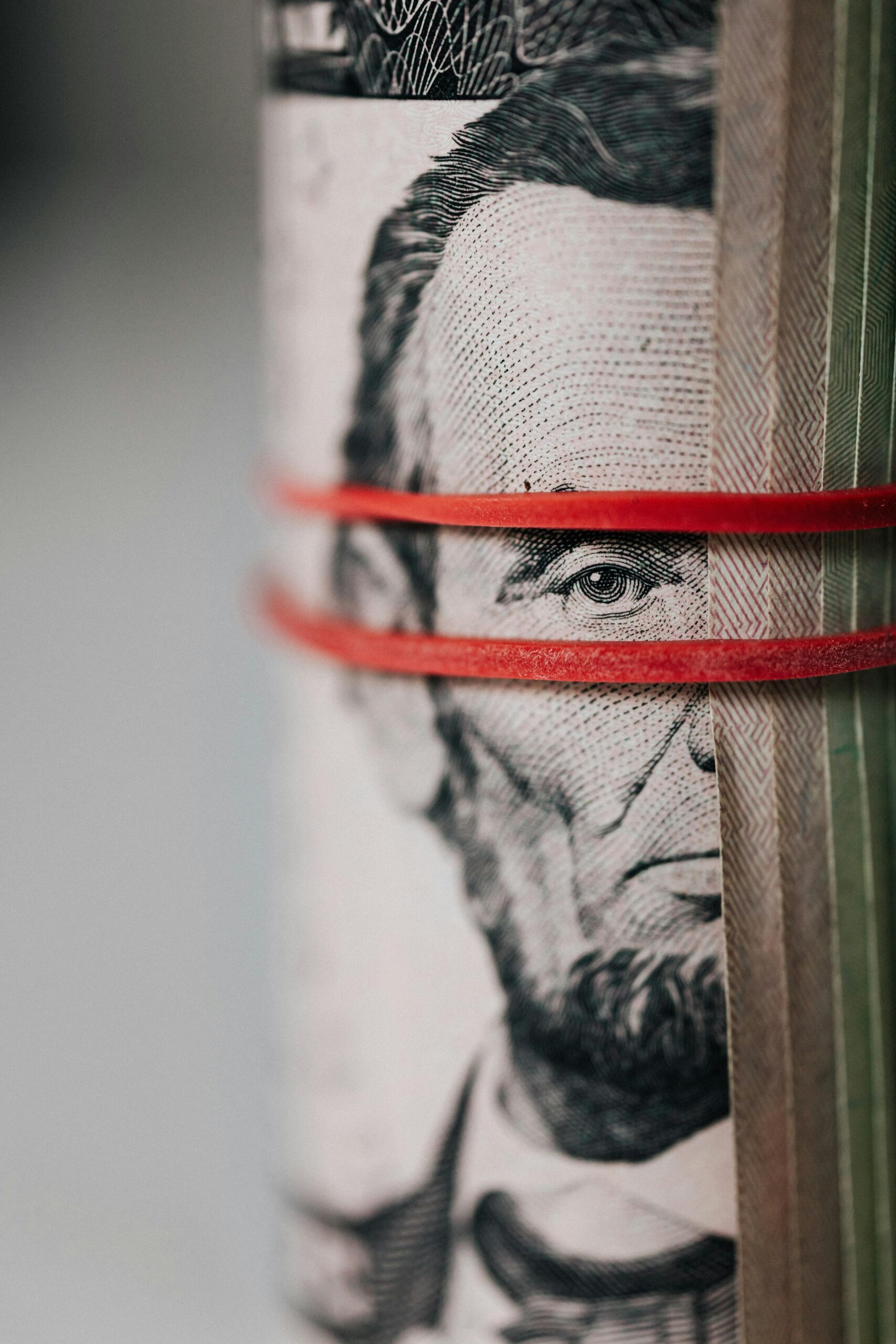
When inflation was running wild, the Federal Reserve attempted to cool the market by increasing interest rates. It was believed that by reducing rates, overall demand would be tempered. Using the supply-demand principle of basic economics, it was hoped that by making it more expensive to borrow money, people would start purchasing less, reducing demand and stopping runaway inflation.
Since the summer of 2023, interest rates have been kept around 5.5%, which is higher than the levels from the previous ten years. But, with inflation cooling, it appears the Federal Reserve is now open to lowering interest rates. Already, the Fed has telegraphed that rates will be cut as early as September.
According to a Morningstar report, Fed officials are expected to “deliver hefty cuts” over the next few years. The Federal Reserve rate could drop to 1.75% by the end of 2026.
The Federal Reserve Bank of St. Louis is making a similar prediction. Their forecast chart calls for interest rates to drop to 4.1% in 2025 and 3.1% by 2026.
So, by almost all accounts, interest rates will drop. But what will this mean for your industry?
Lower interest rates: the impact on manufacturing
Whether manufacturers produce massive equipment or small components, they are impacted by interest rates. Demand for their products will fluctuate quickly after interest-rate hikes are announced, as buyers try to make purchases before the increases take effect. When high rates are in play, consumers and businesses often reconsider large purchases.
High interest rates have clear implications for manufacturers producing large, expensive products. However, the impact also affects makers of small parts and components, who rely on orders from larger manufacturers. The components they produce may not be expensive, but demand for the final product could decline when interest rates are high.
Alternately, when interest rates are low, manufacturing companies experience high demand. It is far more affordable for customers to borrow money, which means large-scale orders, often totaling millions of dollars, can be reduced by tens of thousands.
With an expectation for lower interest rates in the next few years, customers may delay their orders. Instead of ordering now, they may wait a year or two, expecting that by mid-year 2025 or 2026, the cost of borrowing will be much lower. Potentially, this could create a lull for the remainder of the year and a rapid increase in activity once low interest rates are in action.
Lower interest rates: the impact on construction
The construction industry, whether it’s traditional construction or offsite construction (also known as modular), has a unique, two-fold relationship to interest rates. Builders are directly impacted by interest rates, as they often borrow money for materials, tools, and development property. The industry also relies on a consumer base that is heavily influenced by interest rates. Construction (particularly residential) needs homebuyers, but with high interest rates, consumers hesitate to buy homes.
Recently, the construction industry has struggled to maintain growth, although total output remains relatively high. Throughout most of 2022, roughly 1.6 to 1.7 million privately owned housing units were under construction, according to the Federal Reserve Bank of St. Louis. The number has stayed steady, but it has dropped over the past year, from nearly 1.7 million to under 1.6 million.
According to a report from Bluebeam, a construction software company, “higher interest rates have completely frozen the owner-occupied residential construction market.” However, if rates come down, as expected, we could see increased demand for new construction.
Lower interest rates could also create more demand in commercial construction. High rates create a barrier in commercial building, which has projects that are far more expensive (typically) than residential building. With lower interest rates, we could see refreshed activity in commercial construction.
Reduce your impact with Elevated
No matter what the future holds, Elevated Industrial Solutions can be your partner in the manufacturing and construction industries. We understand the needs of dynamic companies like yours, helping you make the right decisions about your company, its processes, and more. Our solutions include coating and finishing, industrial supplies, compressed air systems and services, and assembly tools and services.