Protect your workforce with Greentech for better air
Air may be colorless, but it’s not always odorless. Lingering smells — like fish odor at a processing plant or dirty diapers in a daycare facility — can han gin the air, impacting worker safety and productivity while repelling guests and future workers. Worse, air can carry harmful contaminants without anyone noticing, such as germs, mold, dust, chemicals, spores, and other pollutants. Air carries airborne viruses, too, that can make us sick, including COVID and bacteria.
But now, there’s technology available to protect your workforce, removing odor, pollutants, contaminants, and pathogens. Greentech Environmental (Greentech) sells filters, filtration systems, and purifying equipment to reduce and remove odors as well as keep your workforce safer. And the Greentech team’s approach, including their dedication to research, provides many ways to prevent air from hurting your customers and employees.
About Greentech
Greentech, a leading air-purification company, was founded in 2009 in Johnson City, Tennessee. They have a variety of purifiers and accessories that are ideal for numerous industries, but they also have products for home use, too.
Multiple ways to remove odors and pollutants
Greentech takes an innovative yet intuitive approach to air purification. Instead of focusing on a single technology, they have a multifaceted approach to air purification. Their products use advanced technologies that include treated filters, bipolar ionization, activated oxygen, and photocatalytic oxidation.
ODOGard
One of their most innovative products is the ODOGard filter, which destroys odors at the molecular level. With a unique coating, ODOGard filters create a covalent bond with the odor molecules, essentially changing the molecular structure to eliminate the odor. This method of odor removal is entirely safe, creating an odor-free environment without the use of heavy masking scents.
Passionate about research
Greentech cares deeply about ensuring its products are effective, which is why its employees have rigorous testing standards, use outside testing agencies, and conduct so much scientific research. Employees want to make sure their products do exactly what they claim, even in the environment where their products are being used.
Reducing bacteria, mold, and COVID in schools, medical facilities, hotels, and offices
When it comes to educational facilities (schools, daycares, etc.), medical facilities, hotels, and offices, you want a system that keeps your workforce and clients (students, patients, customers, or guests) safe. In all of these places, odor-free rooms also make them more inviting. Because let’s face it, the odors especially in daycares and schools can be less than desirable.
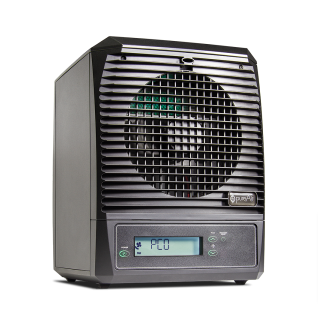
Greentech has portable as well as commercial solutions, including portables and wall mounts. The Active HEPA+ Pro, Active HEPA+ Room, pureAir 3000 MERV+ With Ozone, pureAir 3000 MERV+ No Ozone, 750+ Wall Mount, and SOLO. There’s also an HVAC option where odors and more are eliminated.
Together, the unique combination works to reduce airborne volatile organic compounds (VOCs), allergens such as pollen and pet dander, and odors caused by mold, bacteria, and other pollutants. And the newest product, the Active HEPA+, has been proven to deactivate 99.98% of SARS-CoV-2 from the air.
Let your students, patients, customers, and guests breathe better.
Removing odors in the cannabis industry as well as particulates
Cannabis cultivation and harvesting can be smelly. Many states have or are introducing laws to reduce odor from permeating buildings, impacting neighborhoods. Removing that odor with Greentech is possible.
But it’s not just odors wafting in the air. Grinding leaves and processing the plants can lead to employee breathing issues. Forbes indicates in Massachusetts, a worker died from breathing cannabis dust.
Greentech filters are ideal for cannabis production, a process in which harmful chemicals and air contaminants can become a constant safety concern. According to Greentech, their filters control odors over a longer time and are proven to remove “almost 2.5 times the number of volatile organic compounds (VOCs) than carbon filters, creating a cleaner environment for employees and neighbors.”
Breathe better air
Greentech has options to help you, your customers, and your employees breathe easier. If you’re not sure which product is right for you, Elevated Industrial Solutions can help. We have the background and information needed to get you the product or products that remove odors and eliminate bacteria, mold, allergens, and COVID.
Contact us today and we’ll make sure you have the right Greentech products for your exact needs.