Door and window installations
Door and window installations are the bread and butter for construction companies and general contractors. New construction and replacing windows and doors can be lucrative. But the industry is highly competitive. How can you differentiate your business from your competition to get those good-paying jobs? And how can you keep installation for your windows and doors low?
Flashing and sealants help give your customers the value and quality installation they expect, propelling you above your competition. Plus, these products are cost-conscious, especially when it comes to eliminating the need to do a project over.
At Elevated Industrial Solutions (Elevated) we list our favorite door and window installation products for flashing and sealing … as well as why you may need one versus another.
Flashing solutions
You probably know this, but it merits revisiting. The first line of defense for air and water intrusion is a good seal on the full untrimmed opening for a window or door (also known as the rough opening). When flashing is installed and sealed correctly, water is directed away from the window to keep a home dry and eliminate rot, mold, and mildew. But not all rough openings are created equal (different materials, sizes, shapes, etc.).
Flashing typically comes in three varieties with these advantages and disadvantages:
- Metal flashing is durable, but not as flexible
- Vinyl flashing is flexible, but not as durable
- Tape flashing is easy to install, but often not as durable in hotter areas
- Liquid flashing is a newer innovation in flashing
Find the right flashing for your project from two top brands known for durability and quality. Both Protecto Wrap and OSI products meet local code requirements and national building standards while providing long-lasting performance your customers can count on that won’t break the bank. When they’re used, your jobs will be known as high quality … while reducing long-term liabilities from failure.
Some of the products below may even surprise you!
Protecto Wrap
Protecto Wrap has waterproof membranes that provide high-quality waterproofing. They’re even easy to install. Plus, they have durability and staying power – a preference for construction workers and general contractors since 1952. Here are a few of the products we think are some of their finest:
BT20XL butyl
This 20mil peel–and–stick, self-adhering butyl (the adhesive component) laminated on a polyethylene film provides a tough, durable, easy–to–apply membrane. The product sticks to most common building materials to provide a tight seal while still enabling joint movement. Best of all, it’s compatible with all types of window construction substrates including wood, wood clad, aluminum, fiberglass and vinyl windows and doors, and PVC.
A 120–day UV resistance aids in weather protection during delays in siding or cladding installation.
Super stick building tape
This tape is a primer-less flashing tape for window and door installations. Easy to apply in all temperatures, great for cold climate installations. The tape has the same benefits of butyl or asphalt-based flashing without the primer or the gassing, VOCs, CFCs, and HFCCs. That’s why construction workers and contractors use this so often – it’s a faster turn-around time and fewer customer complaints when replacing windows.
12-month UV exposure is great for new construction where timelines and exposure times can be longer than expected.
Sill pan flash
This one-piece, continuous sill flashing requires no cuts or “butterfly” corner guards. That means, your installation jobs are faster. Also, most people can install these, reducing the need (and expense) for experts to do the cutting or installation. It even has lower product waste. It’s a great option for those 90-degree corners without adding substantial material to the rough opening dimension.
Sealants
Okay, the flashing is done. You’re not out of the woods yet. You may need a sealant to protect your window or door. When it comes to sealants there are lots of options. A few of these products stand out – handling even the toughest climates and jobs.
OSI
Outside of flashing, OSI has a few sealant products that can handle tough jobs with ease. OSI is approved and recommended by many of the top manufacturers because of its durability.
Quad Max
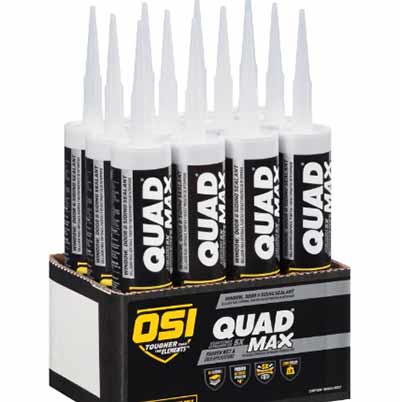
It’s called “Tougher than the Elements” for a reason. This is the premier sealant that can handle the toughest climates. Specifically designed for durability, colorfast, and flexibility, this sealant offers a variety of features, including color matching. OSI’s lab has created exact color matches for all the most popular window and siding manufacturers.
Although some construction workers and general contractors have issues with color matching, that shouldn’t stop you. We stock 30+ options, including the most popular colors in use today. And because we’ve been in business since 1955, we can help select the perfect match for whichever window or siding you’re installing.
Quad Foam
This product is insulating foam for windows and doors. Quad Foam accurately and completely fill voids around windows and doors without stressing or racking. Using an applicator, you can get pinpoint precision to create a tight seal around these irregular rough openings.
BOSS
According to BOSS’s website, their line of products is engineered to the highest quality to ensure maximum performance for the industrial, construction, pool and spa, HVAC/R, manufacturing housing, and RV markets.
363 Acrylic Latex
BOSS 363 is the go-to paintable acrylic latex caulking. Low shrink, non-yellowing, and paintable are all characteristics that will keep callbacks to a minimum. It’s versatile caulking that puts the finishing touch on interior trim while making an airtight seal.
Elevated is on the job with you
Construction workers or general contractors, we have tools and equipment to help you finish your projects on time and on budget. Regardless of whether you love BOSS, OSI, Protecto Wrap, or a different brand, Elevated is with you. We have a variety of brands and products to help you solve your specific window and door installation challenges. Our team has the expertise to get you the right supply or equipment every time.
Talk to our experts today to see how we can help you finish your jobs on time and under budget.