We’re your South Carolina partners
At Elevated Industrial Solutions, we take pride in being the number-one supplier of industrial supplies, paint equipment, and compressed air systems. But we’re especially proud of the products and services we provide in South Carolina, the Palmetto state. Our air compressor business, in fact, is formerly known as Palmetto Compressors.
Everything you need for industrial air compressors
South Carolina facility managers are lucky; Elevated has all the equipment and parts in one location, all backed by our expert service.
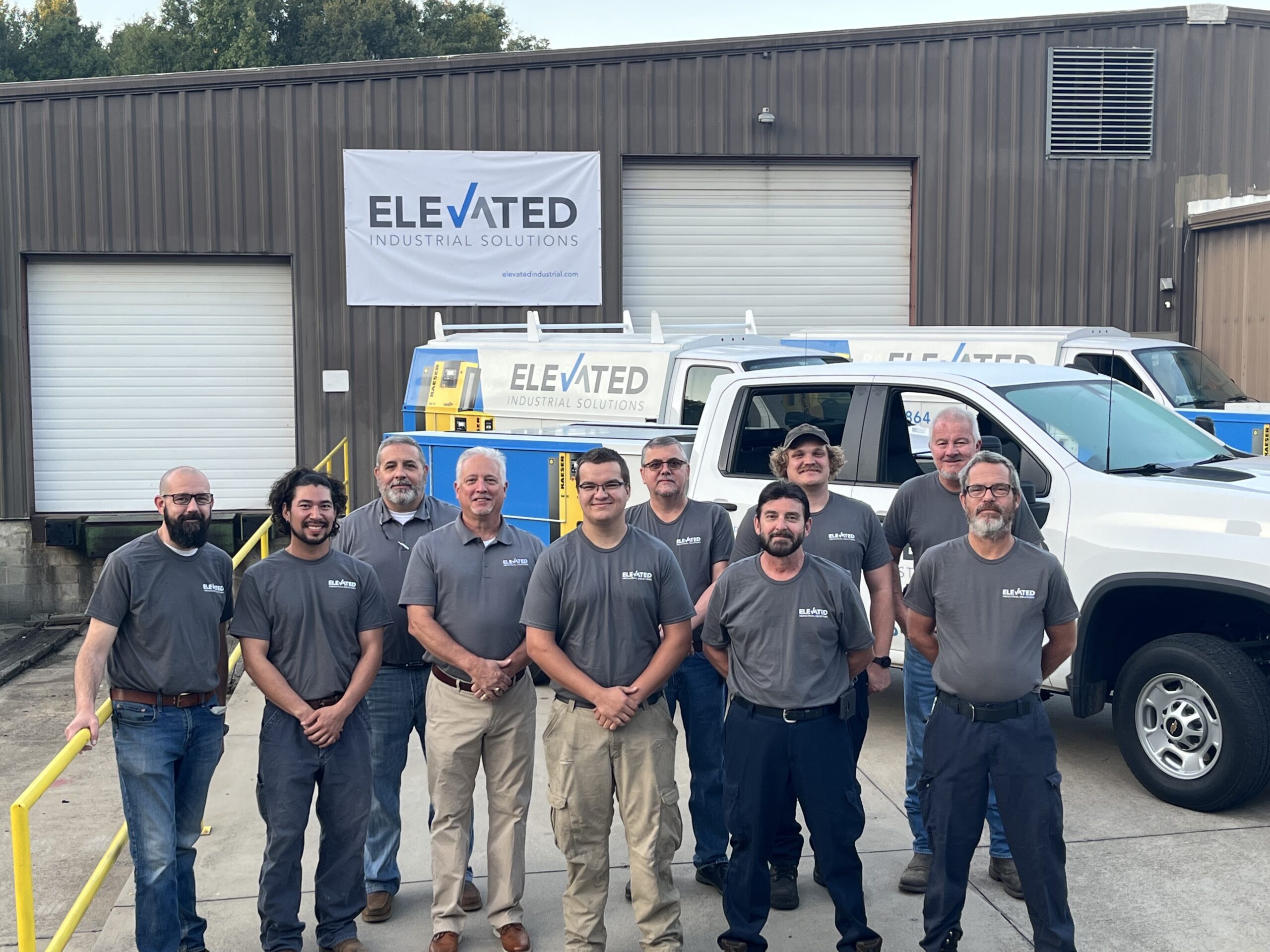
We’re a Kaeser authorized dealer, providing the perfect air compressor for your specific facility. Our specialty is understanding what you’re trying to do and selling you the equipment you need. Plus, we’ll never oversell you. (After all, we want to save energy and money for our customers!) Whether you need a rotary screw compressor or a reciprocating compressor; whether you need vacuums, blowers, or dryers; or whether you need small parts like valves and gaskets, we have it all in one location.
We also offer compressed air system installations that are turnkey. We’ll discuss, design and engineer, plan, and project manage everything to make it as seamless as possible. Our portfolio includes some of the best-looking compressed air systems in South Carolina … if we say so ourselves. (Humble brag.)
Superior service from expert technicians
To be fair, you can find various parts for air compressors just about anywhere. What you can’t find is the exceptional service you’ll get from our team. Our team ensures your facility never goes down and your compressor-related expenses aren’t wasted.
Elevated’s service starts with scheduled preventive maintenance. Our maintenance checklist is comprehensive, encompassing tasks such as changing oil, cleaning the heat exchanger, lubricating the motor drive, and recording system pressure.
But our service doesn’t stop there. We offer air compressor system audits and analysis, including an air audit analysis (ADA), leak audits, vibration analysis, and even provide thermal imaging.
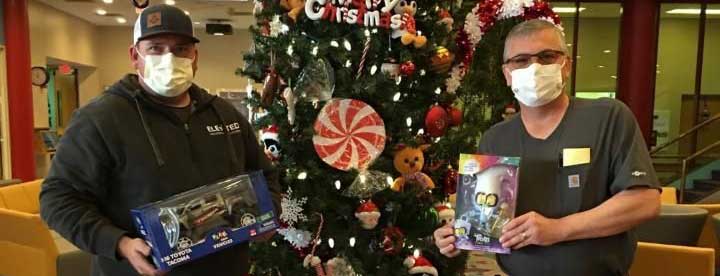
Sure, our expert team has been in the business a long time, but we’re some of the nicest, most-service oriented people you’ll ever meet. We’re also just solid South Carolinians who give to local causes (from the Fountain Inn police to Shriners) and volunteer to make the world a better place, including helping veterans.
Always available to help
When your compressed air system is down, your facility is down. Don’t let production stop just because it’s a Saturday at 10:30 p.m. Get emergency service from our experienced, dedicated team! We’re available 24 hours a day, 365 days a year, including holidays. Our employees travel across South Carolina easily and quickly, from Gaffney to Hilton Head and all points in between … including Greenville, Charlottesville, and Columbia.
More than compressed air systems
We go beyond compressed air, too. We provide industrial supplies such as abrasives, adhesives, tapes, sealants, safety products, and more. And we have coating and finishing equipment for your plant. It’s really one-stop-shopping for industrial companies: great air compressors and service as well as items to keep production running.
Any of our salespeople can offer advice as we’re familiar with the industry. (Part of our company has been around for 60+ years.)
Partners
Our goal is to improve your business. We suggest programs to save your company money, give ideas to improve processes, suggest productivity tips, and more. We’re partners – invested in your business, going the extra mile to ensure you succeed.
That’s why we’re Elevated. We do more in South Carolina. It’s also why we’re tops in the Palmetto State.
When you need preventive maintenance, installation, and parts in the Palmetto State, contact your South Carolina Kaeser distributor today! Plus we can help with industrial supplies and paint equipment.