Save money on your compressed air systems
Depending on the size and scope of a factory, assembly plant, or manufacturing facility, the energy bill could be over $10 million a year. For some facilities, an energy bill of $1 million isn’t unheard of.
Typically, a large portion of this bill comes from air compressors. The Department of Energy estimated that compressed air could account for roughly 10% of electricity consumed at a facility. For some locations, it could be as high as 30%.
According to a scientific review conducted by Malaysian researchers, “Only about 10–20% of total input energy is utilized for useful work in compressed-air system.” This means for every $1,000 spent on compressed-air energy, only $100 to $200 is actually used to power machines and tools.
The numbers can be complex, but the overall point is simple: running an air compressor is expensive. Therefore, you have to get the most from your system. There are many strategies for compressed air savings, including rebates and incentives from state governments.
1. Work with the right installer
Arguably, the most important step, as it impacts all other factors, is that a facility must work with the right installer to bring the highest compressed air savings. An experienced, trained, and knowledgeable compressed air installer can examine your air needs and make quality recommendations to ensure the best results. If needed, they can conduct a thorough audit of your current system.
An air systems installer can work directly with a plant manager and ownership team to make strategic recommendations and ensure successful installation. They can suggest proper equipment for longer lasting energy savings as well as design and install a system that provides maximum efficiency. Installers, especially those who have worked in your industry, will recommend the best placement for air drops, the proper size and number of air compressors, and will consider the cost and value of your system.
Also, an installation professional can recommend changes and custom engineering solutions, helping facilities overcome barriers to efficiency, such as dirty environments or complex facility layouts.
2. Ensure you have the right machines
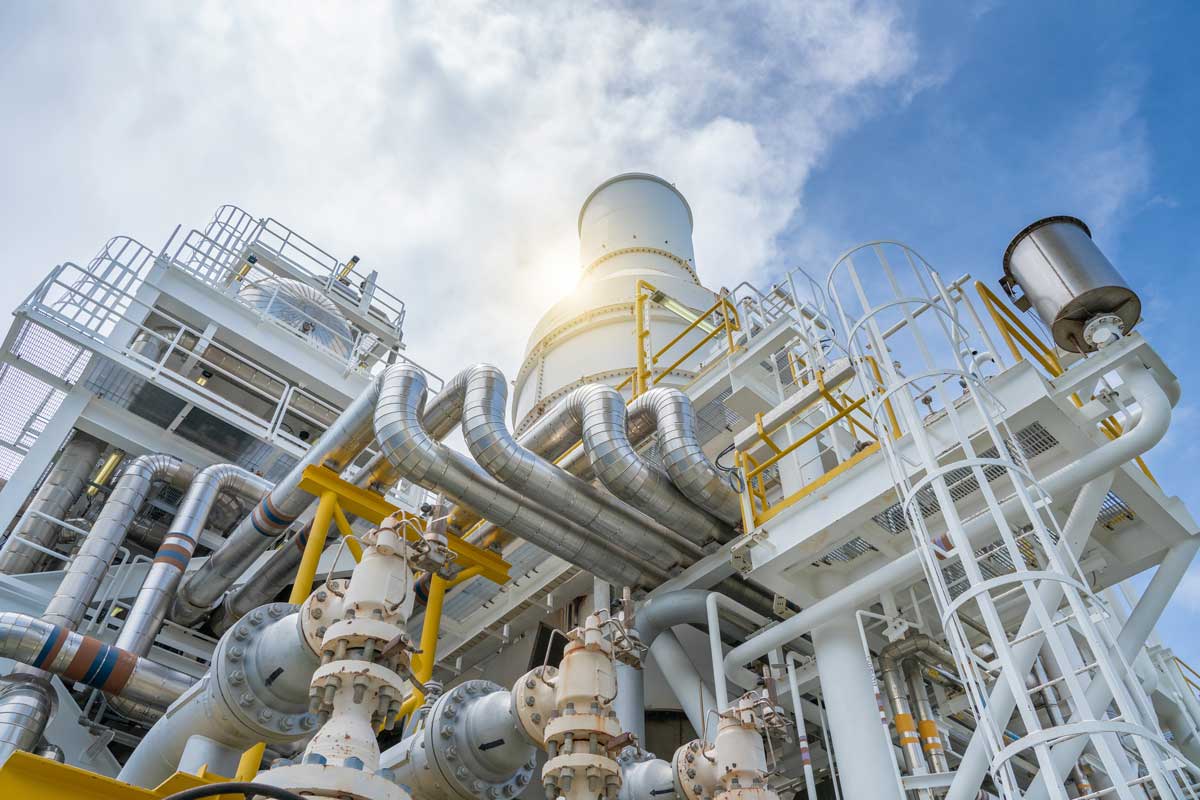
Before a facility can begin maintenance and apply for rebates, it needs the right equipment. Proper air compressors and accessories from leading manufacturers will ensure a higher level of success, bringing better efficiency and lower costs.
The air compressors should properly match your operations. Each facility has different needs for compressed air; some only need one small air compressor, while others need multiple large-scale machines. The distance from the compressor to the use point, as well as the number of drops and types of tools in regular use, will all impact your compressor selection.
The air system, from compressor to tool, should properly match your needs. It must have the right horsepower and deliver proper cubic feet per minute (CFM) to ensure efficient air use.
Compressed air savings start with the right compressor from high-quality manufacturers like Kaeser.
3. Keep up with maintenance
Maintenance matters. Industrial facilities need proper maintenance for their compressed air systems. Maintenance uncovers issues that may cause your facility to shut down and provides opportunities to make immediate changes to run at peak efficiency.
What will a service team do? They’ll change air and oil filters, add lubricant, replace belts, inspect vents, and more. After all, preserving your compressed air system keeps costs down.
4. See your state’s energy rebates
All states, from California to Maine, provide energy rebates and incentives to private individuals and organizations. When considering energy savings, it helps to look up various incentives, especially when installing new equipment, as many programs make energy-efficient installations more affordable. Some offer down-the-road savings through tax incentives (in other words, pay for the expense now, get a big reduction on your taxes later), while others provide more immediate savings or favorable loan terms. The right compressed air service team will know these rebates well.
The Database of State Incentives for Renewables & Efficiency is among the best resources. This website enables you to find excellent rebates by searching an interactive map. You can select a state and search categories that include biomass, fuel cells, geothermal, and emerging technologies. There is also an energy-efficiency category.
There are numerous incentives for every state. Let’s look at a handful of examples from a few states.
South Carolina
In South Carolina, various programs bring financial incentives and favorable loans for energy-efficient upgrades and installations. For example, there is the Energy Efficiency Revolving Loan Fund, which provides up to $1 million for energy upgrades to commercial and industrial groups.
Ohio
Some areas provide local incentives. Cincinnati, Ohio, provides a good example. They have the Property Tax Abatement for Green Buildings program, which allows for a temporary tax abatement on commercial properties that meet LEED certification standards. This allows for a 15-year tax abatement.
Michigan
In Michigan, manufacturing facilities can take advantage of financial incentives that include the Coldwater Board of Public Utilities rebate program. This program encompasses numerous energy-efficient changes that may not be related to your air system but allow for a reduction in your energy bill. This program includes compressed air systems as well!
Call us for compressed air savings!
When it comes to the right installations, ensuring fantastic maintenance, and getting the equipment, the Elevated team can help. We make facilities more efficient, use less energy, and receive money-saving incentives and rebates! Our team will never sell compressed air systems you don’t need. And with 24/7 emergency coverage, we’re here to help you get your facility running at peak performance.