Testing the paint booth market? How to pass with flying colors
Spray booths, also known as paint booths, are definitely important tools that many industrial businesses use to ensure their jobs are finished right. Having the right one can certainly help you achieve success and keep you from fuming over the results. Like any large piece of equipment, you will want to tailor your booth to suit your specific needs and your physical space. Your decision will include many factors, such as cost, product size, desired finish quality, and more. Fortunately, many configurations are available, so you’ll be able to choose the setup that best fits your application. With a little research, we’re sure your spray booth requirements will help guide you to the best decision. Then, you can “go with the flow.”
Consider this article a primer for your paint booth decision. Let’s look at various paint booth configuration options and their features. Here, we’ll be checking out products from two high-quality companies, Rohner and RTT Engineered Solutions (formerly Col-met). They both offer far more options than can be covered in one article, but this blog post will give insight into various available styles and their strengths and weaknesses.
The rock band Queen has told you for years, with their song “Bohemian Rhapsody,” that, “Anyway the wind blows, doesn’t really matter to me.” It doesn’t sound like they were under pressure after all, but they must not have been in the market for a quality paint booth either!
Suppliers
Here’s a brief introduction to the two outstanding suppliers covered in this article.
Rohner
When it comes to manufacturing paint booths, industrial spray booths, truck booths, large equipment, and custom paint booths, Rohner is a global leader. They offer spray booths that have been thoughtfully designed for an assortment of applications. Rohner products have been engineered with efficiency, safety, and cleanliness in mind. These booths feature high-quality materials and industry-leading technology. Also, their products are proudly made in the USA.
RTT Engineered Solutions (RTT)
RTT boasts top engineers in the industry, which means they’re ready and able to deliver creative solutions for your company’s requirements. RTT offers a line of energy-efficient, high-quality, and environmentally-optimized paint booths, addressing a broad range of applications. Their booths are easy to install, efficient, and have you covered for both solvent and water-based coatings.
Now that you’ve met the players, it’s time to look at some configurations.
Open-face booths
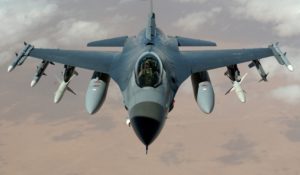
One popular type of paint booth is the Open-Face Paint Spray Booth. With this style, the airflow enters from the front and moves through the work area into a filtered-exhaust chamber at the rear. Once it arrives there, it’s drawn up through an exhaust plenum where it is discharged from the exhaust stack into the atmosphere.
Rohner offers these booths as an efficient and economical method of applying paint to various product sizes. Access is easy, too. They even come with modifications – retrofitted with supply filtration and doors.
RTT refers to their open-face booths as Open Front Booths. The company provides a line that supplies cost-effective solutions for batch applications and conveyorized operations. Possessing a good, flexible design and solid build quality, it’s worth taking a look at the booths that RTT has available to you. They can produce custom sizes and designs based on your location’s specific needs (including conveyor and crane slots/openings).
Open-front bench booths
Another useful booth option is the Open-Front Bench Paint booth. RTT manufactures booths in this style, handy for applying paint to small- and medium-sized parts. It’s a variant of their open-front booth design. These booths are great for batch production systems, and many smaller shops love this model for painting limited numbers of small items. These booths come in an array of standard sizes to maximize your floor space (and custom sizes are available too). Air flow enters the open front of the booth, continues through the working area, and into a filtered exhaust chamber at the rear. Once there, the filtered exhaust air is drawn into the exhaust plenum and discharged through the exhaust stack into the atmosphere.
Downdraft booths
Let’s switch gears and talk about Downdraft booths. Due to their design, downdraft spray booths can produce clean finishes. They also provide superior control of the airflow. This style efficiently handles overspray and can reduce the time you spend on prep. Less overspray waste, improved finishes, and better airflow are just a few reasons you’ll find them in such places as first-class auto-body shops and specialty vehicle places. They function by taking in air through the ceiling and moving it down through the floor where it works its way into the exhaust chamber. One thing you should know — this layout can carry supplementary expenses; for example, construction may be required for the exhaust plenums. Also, downdraft booths typically require about a third more air volume to operate than the cross-draft configuration. That means you’ll see a corresponding increase in operational costs too.
You’ll find that Rohner supplies full Downdraft booths. They have an assortment of sizes and even expandable configurations. Rohner also has solutions for your custom finishing requirements and large equipment and truck needs. You’ll find their product line of these popular downdraft booths out in the world, working in conveyorized paint shops, laying down beautiful automotive finishes at body shops, and even spraying aerospace and oversized parts.
When it comes to downdraft booths, don’t think that RTT is sitting this one out! They also offer a wealth of solutions, including downdraft trucks and large equipment booths. The RTT EZ Pit Downdraft line is a popular choice for applications in the automotive industry. They come in a variety of sizes and their offerings include Standard Duty, Heavy Duty, and Xtreme Duty. Whichever duty calls … they have you covered. There are options available concerning the pressurized, non-pressurized, solid back, reverse flow, and drive-through set-ups. They have modified and industrial selections, too. The modified versions can be found servicing such industries as truck, rail, and aviation, along with a host of other large-scale finishing situations. Their industrial booths are completely customizable. They can be constructed in all manner of sizes and configurations based on your individual needs.
Cross-draft spray booths
Depending on your business needs, a cross-draft booth might be the way to go. They’re extremely popular and typically offer increased affordability combined with a more straightforward installation. Of course, every design has advantages and disadvantages. With the cross-draft layout, overspray and dry-spray can lessen the quality of your finishes. These booths can also increase the risk of contamination. Due to the horizontal airflow, you’ll have to be concerned with floor contamination. If your business demands an extremely high-quality finish, you’ll probably want to go back and take another look at the downdraft section!
Make no mistake, cross-draft booths are wonderful choices for many companies, and fortunately, Rohner has multiple options. Their standard cross-draft design works by drawing non-pressurized, and fresh filtered air out of the supply plenum. The air then flows horizontally throughout the complete work area. It exits through a wall exhaust plenum or pant leg on the far end. This set-up is excellent for finishing an assortment of products both big and small. They can even be set-up as drive-in/drive-out, or flow-through operations. Rohner has efficiently filled the needs of heavy-equipment customers with the scalability and low operating costs for handling heavy equipment. These cross-draft booths are excellent choices for fleet refinishing, providing an automotive-grade quality. Recreational vehicles (RVs) also benefit when collision repairs are necessary.
If the standard cross-draft set-up isn’t quite what you need, Rohner may still be able to save the day with one of their modified cross-draft paint spray booths. These modified versions improve the airflow by guiding the air down from intake filters in the ceiling and drawing it to the back before exiting through the exhaust plenum. With this combination, you’ll receive some benefits from both the downdraft and cross-draft arrangements. Additionally, these can be configured for drive-in/back-out and flow-through applications. Rohner has found clients for their modified cross-draft spray booths ranging from aerospace components (for reduced chemical exposure to the operator), robotic coating applications, and military maintenance sites, where customers take advantage of the extra-wide doors to deal with huge and heavy pieces of machinery. They also offer industrial options.
You’ll discover that RTT has extensive experience and solutions in the cross-draft market as well. Their EZ Classic line of cross-draft booths gives you easy installation (as you might have guessed by the EZ in the name!). Featuring a number of configurations and sizes, you’re likely to find economical answers to your spray booth needs. RTT also provides a line of truck and large equipment booths for various industries. Once again, you have your choice of pressurized, non-pressurized, solid back, drive-through and reverse flow, and their Standard Duty, Heavy Duty, and Xtreme Duty options.
Side downdraft spray booths
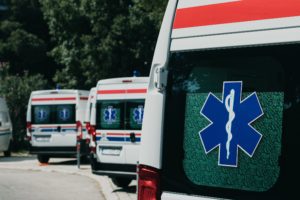
Another option to consider is a side downdraft spray booth. These have some of the same benefits as the aforementioned downdraft style. This design draws air from the ceiling but exhausts it from the sidewall. You may find this choice appealing as it prevents you from extensive (and expensive) concrete floor modifications. However, the additional ductwork required can add costs. The gravity-assisted airflow is a huge benefit to this design. It provides a nice, even pattern of airflow. With this layout, you’ll find more uniformity in your airflow versus the cross-draft arrangement and better contaminant control. The side downdraft style may be the way to go if you’re aiming for a finish comparable to a downdraft booth but don’t want to (or can’t) modify your facility to accommodate the downdraft model. It may also work best due to cost savings. Like all of the other booth options, you do need to be aware of potential issues such as exhaust fans and penetrations in your roof impacting overall cost. Employees may also be annoyed by “wearing” overspray, needing additional gear to keep them safe.
Once more, if the side downdraft style is for you, Rohner has options. They carry a line that can be designed for both flow-through, or drive-in/back-out production lines. Delivering good airflow in large spaces, you’ll see this style employed for tasks such as aircraft finishing. It’s also a natural choice for heavy equipment, which may require the downdraft level of finish while avoiding the concerns of testing the structural rating of the pit!
Like their cross-draft choices, RTT delivers a product line of economic side downdraft booths. We’ll start with the EZ Side Downdraft line. If you’re not able to install a pit, this can be a truly great option. Yet again, RTT offers these in a variety of configurations and sizes. They come to the rescue for regular applications, as well as servicing the bigger crowd with a line-up of Standard Duty, Heavy Duty, and Xtreme Duty choices. By now, you’ve probably figured out they can provide pressurized, non-pressurized, solid back, reverse flow, and drive-through booths.
Trust Lane for your coating and finishing projects
Not to paint ourselves in a corner, but there are more styles of spray booths that could apply to your specific needs. Choosing the best booth is much like laying down any good paint job … it starts with excellent prep work.
At Lane, we can help you assess your coating and finishing needs as well as understand your company’s goals. We thoroughly listen to our customers as partners, helping you be more efficient and effective. Afterward, we can recommend a product based on our expertise. But we’re not a “one-trick pony,” we provide more than just RTT and Rohner coating and finishing systems. We carry some of the most trusted brands in coating and finishing equipment, as well as abrasives, adhesives, tapes, tools, safety gear, and more. Our goal is to be your trusted partner for every industrial need you have.