Kaeser’s Sigma Air Manager 4.0
We’ve heard it before – you’re doing everything you can to save money on compressed air energy, but it’s not working. You’re purchasing energy-efficient compressed air system equipment yet your energy costs aren’t as low as they could be or maybe even should be. Compressed air systems are comprised of a lot of different equipment which can idle when they aren’t needed. Even though your equipment is energy-efficient your compressor, blower, dryer, etc. are all reacting to the needed output demanded.
There’s another piece of equipment that could help.
Introducing the Kaeser Sigma Air Manager 4.0 (aka SAM 4.0)
The award-winning Kaeser Sigma Air Manager 4.0 (SAM 4.0) efficiently gives you more air for less money while increasing productivity. SAM 4.0 has adaptive controls, predictive maintenance, data storage, and analysis – all while maintaining a reliable, consistent, and efficient supply of compressed air. It’s a device that works with your entire system, but also provides a display to enable you to understand how it’s controlling your system.
Management of your entire compressed air system
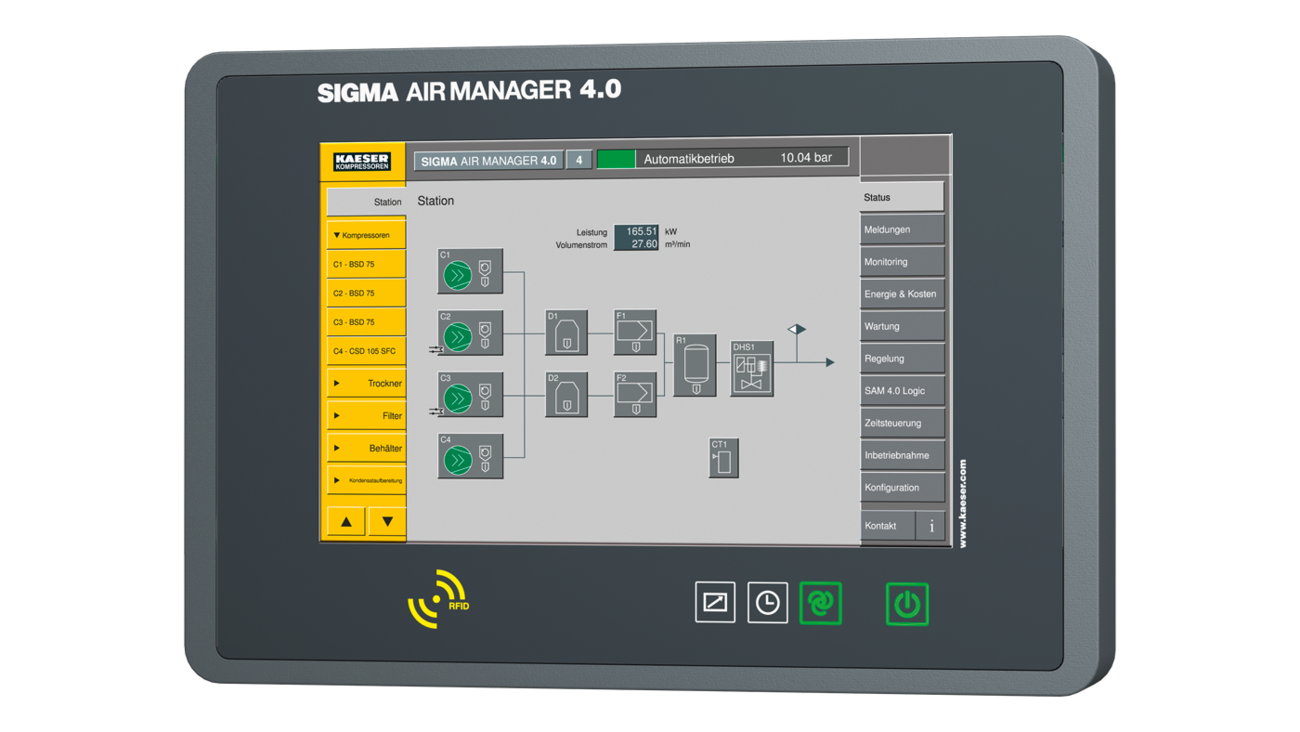
Kaeser’s Sigma Air Manager 4.0 ties in all of your compressed air system equipment including compressors, blowers, and vacuums into a secure Sigma network. That control into one device enables you to manage your entire facility or industrial plant.
Because it controls the entire system, you’ll have steady pressure, energy savings, and efficient use of air!
Messaging and maintenance
In addition, built into SAM 4.0 is a predictive maintenance reminder and messaging abilities. The device communicates exactly what maintenance needs to be performed and when you should do it. No more mind-reading! That functionality obviously makes it easier for you to schedule maintenance, prepare your workforce for maintenance, and get service technicians on the calendar. It also makes it easier for your compressed air service technicians to keep you up and running, eliminating downtime.
These built-in features ensure you never miss preventative maintenance, maximize efficiency, and maximize the life of your compressor and equipment.
Easy-to-use touchscreen technology
SAM 4.0 features a user-friendly 12-inch color touchscreen, which means it’s fairly easy to use. The home screen shows real-time operating status, power consumption, pressure history, flow, and error messages. This data can be accessed anytime and anywhere, giving total control to the facility manager.
Ready to use SAM 4.0?
Are you ready to get steady pressure, receive communication about issues and reports on analytics, and save money on energy? Our Michigan, South Carolina, northern Ohio (near Toledo), and southwestern Ohio (near Cincinnati and Dayton) teams can install SAM and get you up and running. We’ll conduct training to ensure you understand what you’re seeing, too. Plus, we can maintain your system and be there if SAM communicates any issues – 24 x 7, 365 days a year.