Common problems and mistakes when spraying paint
Applying a coat of paint is simple. At least in theory.
In practice, however, making your product look great can be surprisingly complicated, difficult, and frustrating. How can you achieve the best result while maintaining the perfect finish? We have ideas about avoiding common mistakes and problems. Understanding the common issues, including typical problems and mistakes, and taking steps to avoid them will create a foundation for an outstanding final product.
Not reading the product datasheet or setting the spray gun up correctly
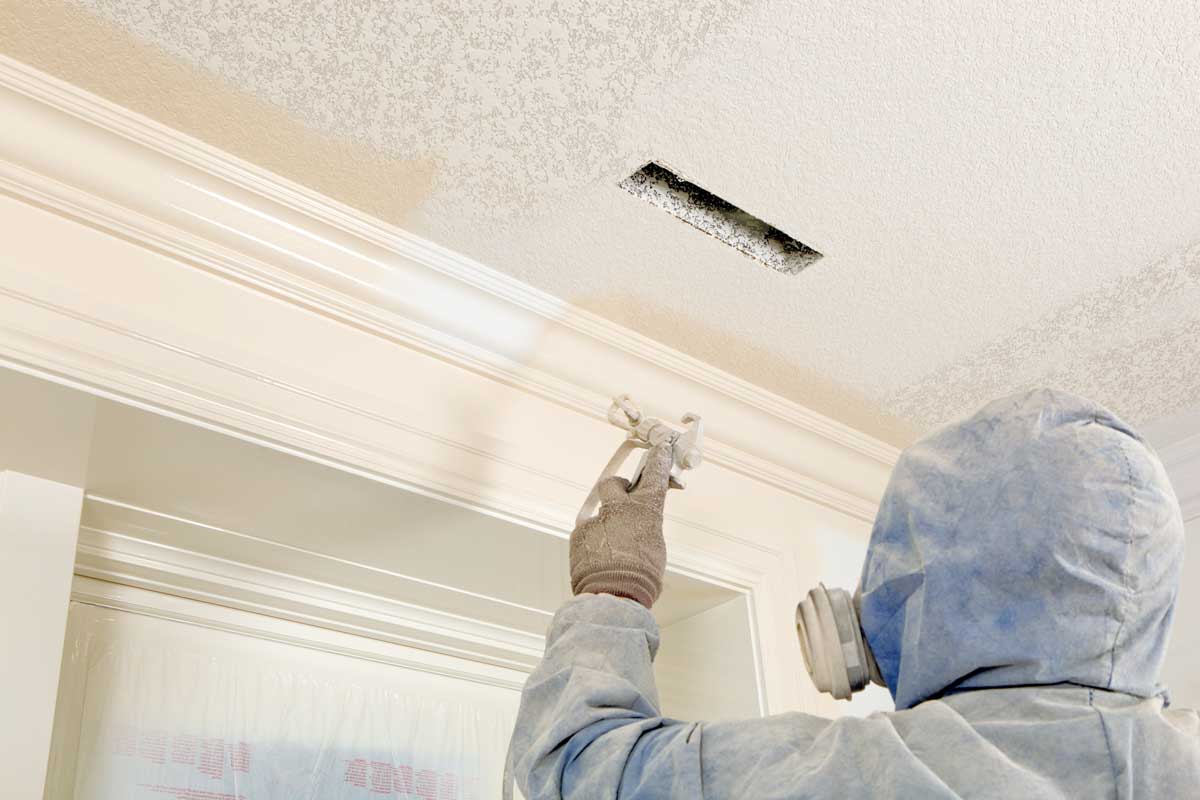
The manufacturer’s technical data sheet provides essential information that helps you create a perfect finish. So, take your time, break out the technical data sheet, and familiarize yourself with the product. You’ll find essential information, such as when to use the appropriate hardeners and thinners, spray gun setup, thickness, drying times, and re-coating procedures.
The spray gun must be perfectly set up to create the ideal paint job. With an improper setup, you’ll see pimples, blisters, fizz holes, oversprays, and runs. Again, the product datasheet will provide the best information on how to set up your system; check it ahead of time to avoid problems.
Not underestimating drying times
Understand the proper drying time for your paint and substrate. The atmosphere, temperature, film thickness, solvent, and more can affect drying times. Don’t get impatient or guess; make it a standardized part of your process to calculate these for the best results. Get more ideas about drying times.
Not providing the appropriate air pressure
The right air pressure is a fine balance. Too little air pressure from the spray gun, and you’ll see pitchy patterns, more paint applied to the outer circle (rather than the center), and uneven paint distribution. Although these problems could be caused by other issues, such as worn-out nozzles, they generally indicate weak air pressure.
Too much pressure is also a problem. Some people try to increase the air pressure, thinking this will speed up the process and enhance efficiency. However, it can lead to oversprays, excessive paint use, and increased wear on the spray gun.
The trick is to work at the lowest required pressure to create a high-quality finish. Start at the lower end of the pressure range, then steadily add pressure until you have the ideal paint distribution.
Unmaintained equipment
Your spray system, including the hoses, guns, and filters, should be properly maintained. The filters are especially important, as dirty filters cause pressure drops, reduce efficiency, and create a poor final coating. Dirty filters will release debris, landing on the finishing and creating a substandard product.
Poor adhesion
Poor adhesion, when the paint does not properly cling to the material being sprayed, can be caused by various issues. For example, solvents in the topcoat may penetrate through areas of the undercoat; this could be caused by an unsuitable primer. Peeling could also occur, which is often caused by insufficient prep time or the wrong primer. Another problem is wrinkling or lifting of the paint, which occurs when solvents in a new finish interact with the old finish. Issues may arise if you don’t give time to cure. You may even have issues if you don’t clean or prepare your substrate.
Whether you see chipping, wrinkling, or parts of the paint lifting in feathers, you’ll want to re-examine your entire paint process, especially the curing, primer, and dry times.
Defective finish texture
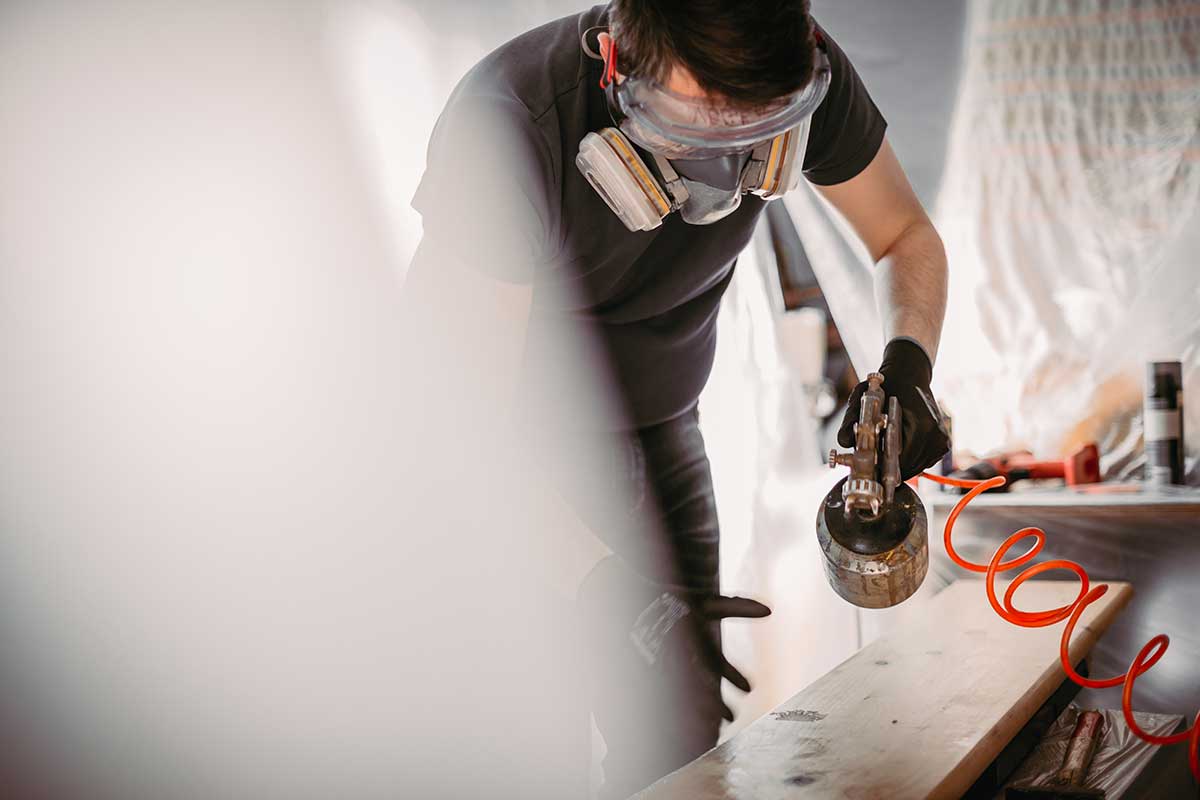
You’ll know a defective finish when you see it. You may see air trapping, cracking, or webbing, which could have a spiderweb appearance or become “crow’s feet,” which are cracks in the top layer. You could also have dimpling or a grainy finish. All of these issues may be unnoticeable from a distance, but they are problems that can be seen when viewing the product up close.
Like poor adhesion, a bad texture can be caused by different issues, depending on the specific texture flaw. For instance, if you see a grainy finish, it could be caused by spraying too far from the substrate. Essentially, the paint is atomizing and drying before it lands. Or, if you have a gritty finish, you may have a dirty system or working in a dusty environment.
Discoloration
Discoloration, darker or lighter than your intended finish or coat, can also negatively impact your product. Your customers expect a uniform color, but various issues can cause the final coat.
One of the more common problems is a blushing or cloudy appearance in the paint. This is often caused by spraying in a humid environment, which causes the solvents to evaporate and traps moisture in the paint layer.
Another issue related to discoloration is bleeding, a yellowish stain that appears in the topcoat. This can happen because of too much hardener, insufficient mixing, and priming before the filler is completely cured.
Not getting the right equipment
There are many choices for spray guns and spray systems. More complex systems come with options for hoses, pumps, mixers, and more. Choosing a low-quality brand just because it’s cheaper can impact your project. Not getting accessories that work together can just waste time and money.
At Elevated, we can recommend options, parts, and processes that improve your product, increase longevity, and build your industry reputation. Our experts can visit your location to provide ideas to meet your business goals.