Increase paint transfer efficiency
Paint transfer efficiency is critical to your industrial painting, whether you’re painting ambulances, marine vessels, pallets, or something else. Increasing the transfer efficiency saves money and meets state and federal regulations. Plus, it could even make your workforce more productive.
What is paint transfer efficiency?
Commonly referred to as “TE,” transfer efficiency is a calculation of how much paint spray covers a component, and how much is wasted. The higher the percentage, the better. But achieving high TE rates is extremely difficult, especially if your team is using mismatched, older, or insufficient equipment.
Understanding the standards
There are two standard models used for measuring transfer efficiency when painting equipment and parts:
- American Society for Testing and Materials (ASTM). This test simulates a conveyor system and generally results in percentages below 50%.
- European Standard EN 13699-1 (EN). The EN test is performed by simply spraying a pattern in the middle of a large part.
The ASTM test almost always results in lower percentages than the EN technique does. For example, a test using the ASTM method may result in a transfer efficiency of 25 to 35%, while the same equipment under the EN test may show 70 to 80%.
Regardless, you must increase transfer efficiency at all times.
Why transfer efficiency?
High transfer efficiency is important for a few reasons. First, it’s essential to your bottom line. Suppose you have a transfer efficiency of 15%. This means for every $1,000 in paint, you are essentially using $150 while wasting $850 of paint. If you spend $10,000 coating a line of components, you would waste $8,500! Increasing the TE to an ASTM rate closer to 50% will create significant cost savings.
Second, better transfer efficiency reduces VOC emissions and waste. So it’s better for the environment. But … it’s not just important for air quality or to keep paint run-off from reaching water sources. Keeping your transfer efficiency high will help you stay within regulatory requirements. Learn more about federal standards. As you might imagine, some states (we’re looking at you, California) have stringent laws to protect people, land, and wildlife, including offering paint recycling programs with incentives.
Lastly, having a process and understanding how you’re using the equipment, including taking metrics for paint, increases productivity. That means you could paint more products in less time!
How to optimize transfer efficiency
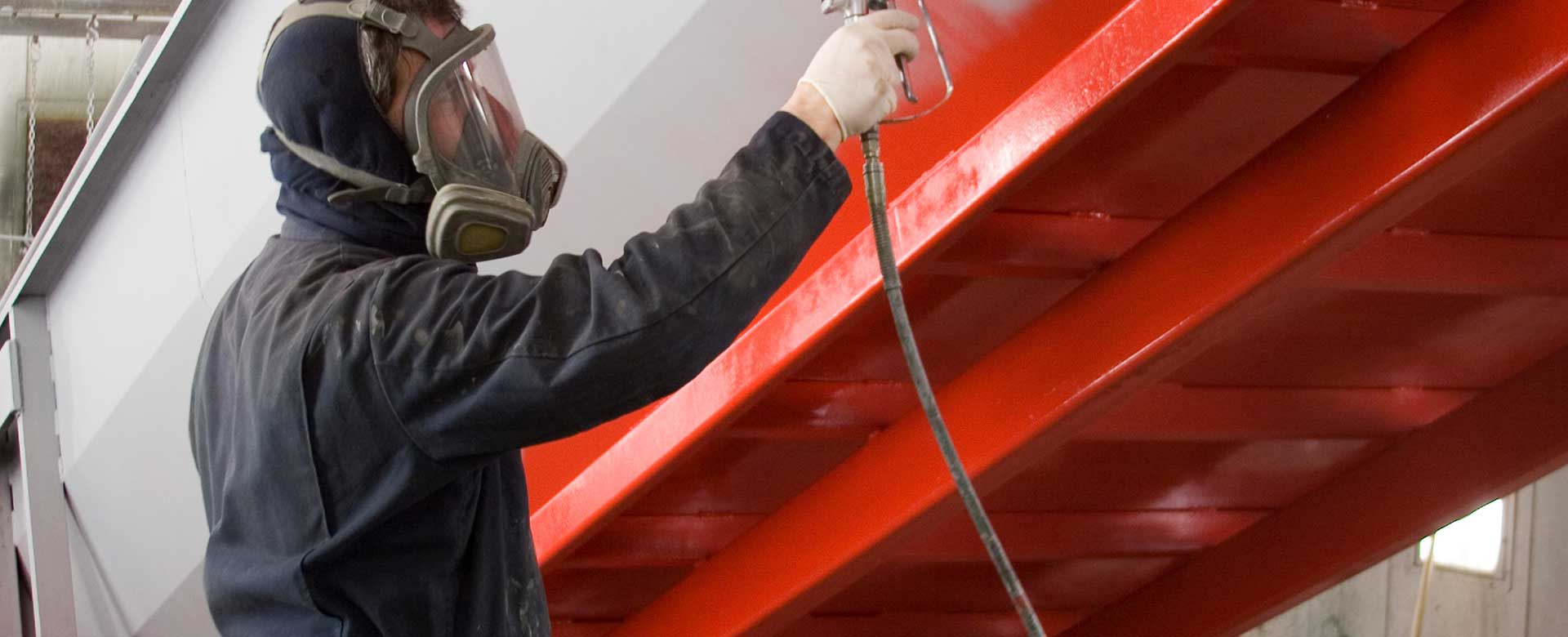
There are many ways to enhance your transfer efficiency numbers, but the most important one is having the right equipment. Optimized equipment for painting, coating, and finishing will help increase transfer efficiency, especially if you have a paint booth or system recommended by knowledgeable industry experts.
Your coat and finish team should also be properly trained. Training team members on proper spray distance, angle (perpendicular coating), and trigger timing will all help your overall transfer efficiency, while also improving product consistency and increasing profit. This can be achieved only through consistent and ongoing training and assessment.
Luckily, Elevated provides that training and documentation, ensuring your entire workforce understands what to do and how to do it. We even offer parts service, replacing parts when you need them.
Get help from experts and the right equipment
Elevated Industrial Solutions is your source for top-quality coating and finishing equipment. Using the right tools and accessories is critical for maximizing transfer efficiency. Not only do we have spray systems, parts, and paint booths available from trustworthy partners, but our team has been implementing coating and finishing solutions across the U.S. We train and provide documentation so your team feels confident and productive.
Let us visit your site and give recommendations.